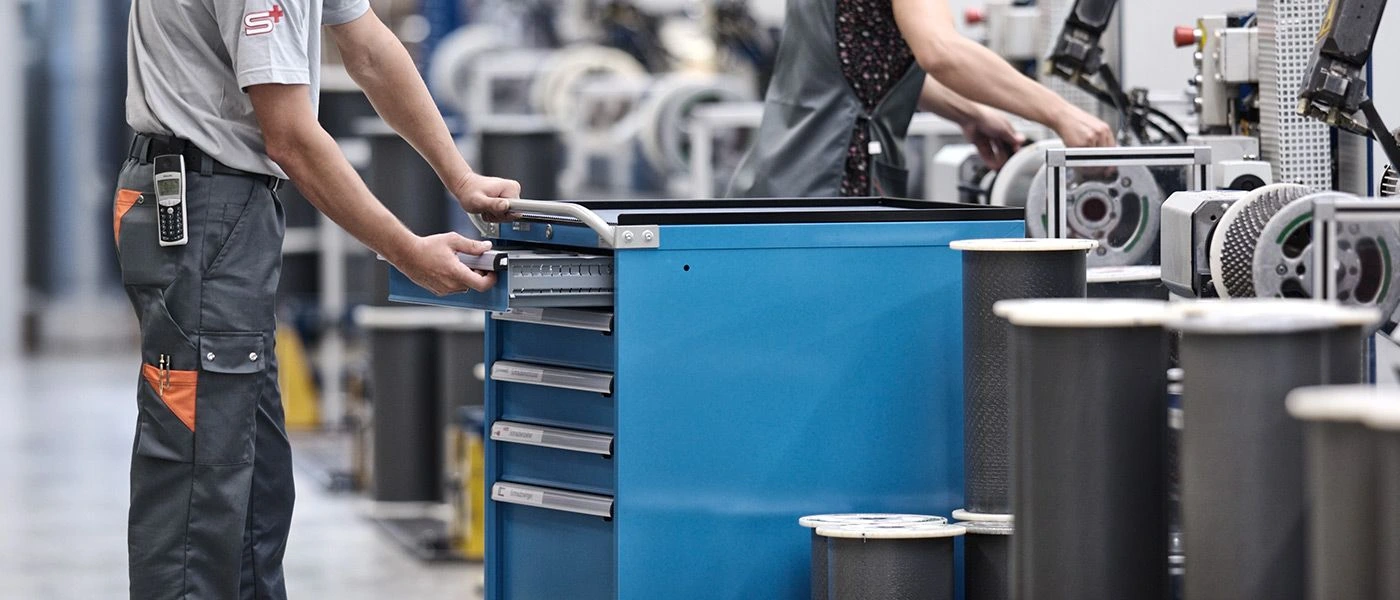
Innovación en el mantenimiento industrial
El mantenimiento industrial ha pasado de ser una tarea correctiva y reactiva, a convertirse en un proceso inteligente, automatizado y altamente eficiente gracias a la integración de nuevas tecnologías. Hoy, herramientas como el Internet de las Cosas (IoT), el mantenimiento predictivo, la realidad aumentada y la digitalización total de procesos están revolucionando el cuidado y funcionamiento de los equipos en múltiples sectores.
A continuación, te mostramos cómo estas innovaciones están cambiando las reglas del juego.
Automatización e IoT El inicio de un mantenimiento inteligente
La automatización permite que muchos procesos de monitoreo, diagnóstico y ajustes en los equipos se realicen sin intervención humana constante. Los sensores conectados a través del Internet de las Cosas (IoT) recopilan datos en tiempo real como temperatura, vibraciones, ciclos de uso o consumo energético. Esta información es enviada a plataformas de análisis que interpretan los datos y detectan comportamientos fuera de lo normal.
Beneficios principales:
Detección temprana de fallas.
Menor dependencia de inspecciones manuales.
Ahorro en costos de reparación.
Prevención de paradas inesperadas..
A diferencia del mantenimiento preventivo tradicional, que se basa en calendarios, el mantenimiento predictivo utiliza inteligencia artificial y aprendizaje automático para predecir el momento exacto en que un equipo podría presentar una falla. Esto se traduce en un uso más eficiente de los recursos y una mayor vida útil de los activos.
Ejemplo práctico: Una bomba hidráulica muestra una vibración fuera de su rango óptimo. El sistema predice que fallará en 15 días si no se ajusta. Se realiza mantenimiento justo a tiempo, evitando daño mayor.
Digitalización y trazabilidad: Control total de los procesos
La digitalización permite a las empresas tener un registro completo y accesible del historial de mantenimiento, piezas sustituidas, responsables de intervención, y más. Esta trazabilidad es esencial no solo para controlar la eficiencia interna, sino también para cumplir con normativas de calidad y auditorías.
-Gestión centralizada de activos.
-Toma de decisiones basada en datos.
-Optimización de rutas de técnicos y tiempos de respuesta.
Realidad Aumentada y Simulación: El futuro ya llegó
Con tecnologías como la Realidad Aumentada (AR) y la Realidad Virtual (VR), los técnicos pueden visualizar el interior de los equipos, recibir instrucciones en tiempo real o incluso entrenarse en entornos virtuales antes de una intervención real. Estas herramientas reducen errores humanos y permiten soporte remoto inmediato.
Impacto en el mantenimiento:
Técnicos menos expuestos a riesgos.
Soporte remoto a distancia con mayor precisión.
Capacitación práctica sin poner en riesgo equipos reales.
En resumen: ¿Qué logran las empresas al implementar tecnología en el mantenimiento?
– Reducción de tiempos muertos por paradas no planificadas.
-Disminución en el costo total de propiedad de los equipos.
– Mejoras en la seguridad del personal técnico.
-Mayor disponibilidad y eficiencia operativa.
– Cumplimiento normativo con evidencia digital trazable.
fuentes:
“How IoT and Predictive Maintenance are Changing Manufacturing,” Manufacturing.net, 2024.
“The Impact of Digitalization on Industrial Maintenance,” Industrial Maintenance and Plant Operations, 2023.